Piastrella
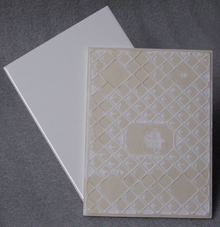
La piastrella (denominata anche "mattonella" o "pianella") è un elemento architettonico usato per rivestire le superfici di pavimento e muri come rifinitura e anche con fini artistici. La figura professionale che si occupa della sua installazione è detta piastrellista.
La piastrella rientra all'interno della categoria dei prodotti semilavorati edili.
Nel passato venivano usate le cementine al posto delle piastrelle.[senza fonte]
Caratteristiche
[modifica | modifica wikitesto]Caratterizzata da spessore ridotto (oggi lo spessore minimo va da 3 a 20 mm), può presentare forme geometriche molteplici (quadrati, rettangoli, esagoni, ecc.), formati variabili (15x15 cm, 15x20 cm, 20x20 cm, ecc.) e può essere realizzata con materiali diversi (laterizio, graniglia, marmo, ceramica, cemento, ecc. ).
In alcuni casi la tolleranza dimensionale della piastrella può essere relativamente alta rispetto alla misura dichiarata, si tratta comunque di decimi di millimetro in più o in meno, in questo caso il lotto di piastrelle riporterà una lettera alfabetica correlata al calibro effettivo e dichiarato del lotto di piastrelle.
La resistenza all'abrasione superficiale della piastrella si misura in PEI (che va da 0 a 5) tramite il quale si misura la capacità dello smalto della piastrella di resistere al calpestio, al passaggio di persone, di mobili o di macchinari, senza perdere le caratteristiche estetiche originali.
La "capacità di attrito" di una piastrella (cioè la resistenza allo scivolamento di un corpo sulla sua superficie) è determinata dal processo di trattamento della superficie stessa, la quale potrà essere levigata, bocciardata o lavorata in modo tale da non renderla del tutto liscia.
Per ottenere piastrelle più resistenti, l'impasto va cotto a temperature maggiori affinché l'argilla solidifichi con una maggiore densità molecolare.
Lavorazione
[modifica | modifica wikitesto]La piastrella più comune si ottiene da un impasto di materiali argillosi e sabbie quarzifere cotto in forni a una temperatura oscillante tra i 1060 °C e i 1220 °C a seconda della tipologia per 30-70 minuti. Quando poi viene lasciato raffreddare, si ottiene un materiale resistente, rigido, non più solubile in acqua, con buona resistenza agli attacchi sia chimici che meccanici.
Le categorie di piastrelle in ordine di resistenza fisica e meccanica:
- Cotto: piastrella a pasta bianca o rossa (il colore dipende dalla composizione dell'argilla). La colorazione rossa è invece data dall'ossidazione di tracce di ferro.
- Monocottura: consiste nel cuocere supporto e smalto in un'unica passata in appositi forni a temperature che oscillano tra gli 1170 e i 1200 °C. Si può considerare come la tecnologia che ha reso durezza ai prodotti per la pavimentazione. Non priva di difetti ad oggi viene considerata per i materiali a basso costo.
- Bicottura: la piastrella viene realizzata in due tempi, dove nel primo si cuoce l'impasto parzialmente, andando così a creare quello che viene comunemente chiamato biscotto, mentre in un secondo momento questo viene dipinto con smalti e passato alla seconda cottura.
- Clinker.
- Grès porcellanato in massa: piastrella non smaltata ottenuta tramite un processo chiamato "pressatura". Può assumere vari colori e texture in base ai componenti utilizzati nella composizione dell'impasto. La caratteristica principale è il bassissimo tasso di imbibizione (assorbimento di acqua) 0,04% che la rende completamente inassorbente. In alcuni casi il grès porcellanato più pregiato viene denominato Marmo di Fabbrica.
- Grès porcellanato smaltato: piastrella smaltata derivante da un processo simile alla monocottura ma con caratteristiche finali tipo grès. Può assumere vari colori in base alle texture utilizzate nella fase decorativa a smalto. Si può considerare l'evoluzione tecnologica della Monocottura.
La posa
[modifica | modifica wikitesto]La posa su pavimento definito "fresco su fresco" (metodo tradizionale ma ormai obsoleto) consiste nello stendere un letto di magrone accuratamente livellato e compresso, con un successivo "spolvero" di cemento. Il magrone è un impasto umido di sabbia e cemento, preparato con una modesta quantità d'acqua affinché abbia la stessa consistenza della sabbia umida, impalpabile ma non fluido. Si posano sopra le piastrelle preventivamente bagnate, livellandole uniformemente; poi si versa una certa quantità acqua sul pavimento e si procede con il livellamento finale. L'acqua penetra tra le fughe e viene assorbita dall'impasto secco, affinché il cemento del magrone e dello spolvero possa far presa. A posa terminata, si passa al riempimento delle fughe tra le mattonelle tramite la boiacca, un impasto semi-liquido di cemento o calce. Con questo metodo di posa si realizzano contemporaneamente il massetto ed il rivestimento, era largamente impiegato con le mattonelle in cemento chiamate "marmette".
Oggi, sia per il pavimento che per la copertura dei muri, prevale l'incollaggio della piastrella con prodotti specifici al fondo solido e asciutto preparato in precedenza e sufficientemente stagionato (massetto); a questo metodo si accompagna solitamente la realizzazione di fughe di larghezza appropriata al tipo e dimensione della piastrella. Questa tecnica ha il vantaggio di eliminare il rischio di presa non avvenuta in qualche punto del pavimento, e risulta più sicura, perché i moderni adesivi contengono speciali additivi che li rendono più elastici e tenaci del semplice cemento. In particolare, il cemento avrebbe scarsa adesione su materiali non porosi come il grés. Il materiale di riempimento della fuga è costituito da miscele in polvere, ottimizzate nel colore e nella granulometria e aventi caratteristiche di elasticità ed impermeabilità migliorabili con l'uso di additivi (solitamente apportati dallo stesso produttore).
Per garantire l'uniformità della distanza fra una piastrella e l'altra i piastrellisti usano distanziatori appositi. Sono solitamente di materiale plastico rigido, con forme a croce o a T, e sono disponibili di vario spessore in base alle esigenze di posa o del cliente. Prima della fugatura finale, i distanziatori più alti vengono rimossi, mentre se ben schiacciati rimangono incorporati nel pavimento sotto la stuccatura.
Il taglio
[modifica | modifica wikitesto]Per il taglio, operazione spesso necessaria lungo il perimetro dei muri, possono essere applicati due metodi:
- Il primo, adatto per piastrelle a bassa durezza e piccolo spessore, consiste nell'effettuare un'incisione per mezzo di un apposito attrezzo, lungo una linea di rottura stabilita; successivamente verrà applicata una piccola pressione sull'incisione che consentirà di spezzare in due l'elemento.
- Il secondo, adatto invece a piastrelle molto dure, fa uso di un disco diamantato inserito in una macchina specifica fissata a un supporto rigido, oppure di una semplice smerigliatrice portatile; spesso però tali arnesi sono complementari tra loro, in quanto la smeragliatrice, indispensabile per eseguire manualmente tagli curvi, lavora necessariamente a secco, producendo parecchia polvere (effetto non dato dalla macchina fissa che lavora a umido), entrambe utilizzano comunque dischi diamantati.
Voci correlate
[modifica | modifica wikitesto]Altri progetti
[modifica | modifica wikitesto]Wikizionario contiene il lemma di dizionario «piastrella»
Wikimedia Commons contiene immagini o altri file sulla piastrella
Collegamenti esterni
[modifica | modifica wikitesto]- Piastrèlla, su Vocabolario Treccani, Istituto dell'Enciclopedia Italiana.
- piastrèlla, su sapere.it, De Agostini.
- (EN) tile, su Enciclopedia Britannica, Encyclopædia Britannica, Inc.
- (EN) Opere riguardanti Piastrella, su Open Library, Internet Archive.
- Guida alla posa piastrelle, su professionepiastrellista.it.
- Associazione Nazionale Ceramica Italiana: Confindustria Ceramica
- Portale De La Ceramica Italiana: Ceramics Of Italy
Controllo di autorità | Thesaurus BNCF 14595 · LCCN (EN) sh85135352 · GND (DE) 4017536-4 · BNF (FR) cb11977297r (data) · J9U (EN, HE) 987007536569505171 · NDL (EN, JA) 00572553 |
---|